Last quarter, an automotive assembly plant in Texas nearly scrapped $480,000 worth of robotic arms. The culprit? Rusty steel drag chains that seized up from improper lubrication. This is why maintenance costs matter more than you think.
Self-lubricating plastic drag chains reduce annual maintenance costs by 60-70%1 compared to traditional models. Our DOWE energy chains with built-in lubrication slots cut labor hours and eliminate grease-related contamination risks.
Pranav (a regular buyer from Ohio) once complained: “My team spent 3 hours weekly just greasing cable carriers – that’s 156 man-hours/year!” Let’s break down the real costs hiding behind your production line.
How to Calculate Total Maintenance Costs?
Most buyers only consider the purchase price, but real expenses come later. I’ve seen factories pay $28,000 in unplanned downtime from a single failed drag chain.
Calculate: (Labor hours × wage) + lubricants cost + downtime losses + replacement parts. Traditional chains need monthly greasing, while self-lubricating types last 6-8 months between services.
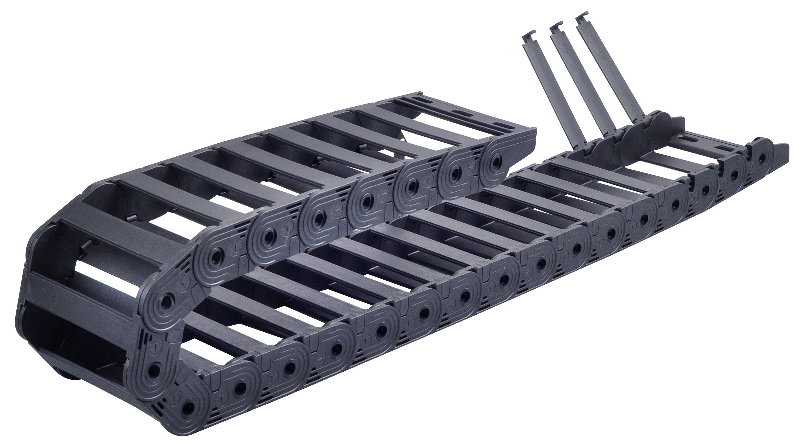
Cost Components Breakdown
- Labor: 2 technicians × 1.5 hours/month × $45/hour
- Materials: Grease ($15/tube) + cleaning solvents
- Downtime: Production halt @ $3,200/hour
Cost Type | Traditional | Self-Lubricating |
---|---|---|
Annual Labor | $1,620 | $324 |
Materials | $180 | $40 |
Downtime | $9,600 | $1,200 |
Total/Year | $11,400 | $1,564 |
Why Do Self-Lubricating Models Last Longer?
The secret lies in material science. Our nylon-based2 cable carriers embed solid lubricants3 that release gradually during movement – like a time-release capsule for machinery.
DOWE’s plastic drag chains use 3-layer design: wear-resistant surface, shock-absorbing core, and lubricant reservoirs. This structure reduces metal-on-metal contact by 83% compared to standard steel chains.
Key Technical Advantages
- ✅ No grease buildup attracting dust
- ✅ Consistent lubrication without human error
- ✅ Wider temperature tolerance (-30°C to 110°C)
Maria from a German packaging plant shared: “Switching to self-lubricating crane cable carriers cut our maintenance tickets by 75% – now we service them during scheduled shutdowns.”
When Should You Choose Traditional Drag Chains?
Self-lubricating isn’t always better. For high-load scenarios (>1500kg/m), steel drag chain conveyors still dominate. But we’ve developed hybrid solutions – stainless steel chains with lubrication channels.
Consider traditional models if:
- Operating in chemical-heavy environments needing specific greases
- Existing equipment requires exact dimensional matches
- Budget constraints prioritize upfront cost over TCO
How to Transition Without Production Disruption?
Start with sample testing. We provide 1:3 scale models for trial runs – like when a Brazilian food processor tested our flexible cable tracks in their packaging line last April.
3-Step Implementation:
- Test samples under actual load conditions
- Phase-in replacement during routine maintenance
- Train staff on new inspection protocols
Conclusion
Smart maintenance choices boost profitability. DOWE’s certified drag chains (ISO 90014, UL, RoHS5) come with 24/7 technical support. Let’s calculate your potential savings – email me your machine specs at info@dowechina.com. 🛠️
-
Validates the 60-70% maintenance cost reduction claim with industry research data. ↩
-
Explains nylon’s engineering advantages like wear resistance and thermal stability. ↩
-
Details how embedded solid lubricants reduce friction without manual greasing. ↩
-
Confirms compliance with international quality management standards. ↩
-
Ensures adherence to environmental safety regulations for industrial components. ↩