Industrial environments demand durability. Corrosion can cripple machinery, delay production, and cost thousands. Let me show you how material choice makes or breaks your drag chain’s lifespan.
Plastic drag chains outperform steel in most corrosive environments, while stainless steel provides balanced strength and chemical resistance. But material performance depends on your specific application and exposure.
Last year, Pranav from Texas nearly lost a $50k automation project due to acidic coolant eating through steel chains. His story taught me why understanding material properties matters. Let’s break it down.
[Table of contents]
What’s the Corrosion Resistance of Common Drag Chain Materials?
No two workshops face identical challenges. From salty coastal air to chemical splashes, your environment dictates the best material choice.
Nylon drag chains resist mild chemicals and moisture, while stainless steel handles aggressive acids and high temperatures. Plastic options like PPA1 excel in moderate industrial settings.
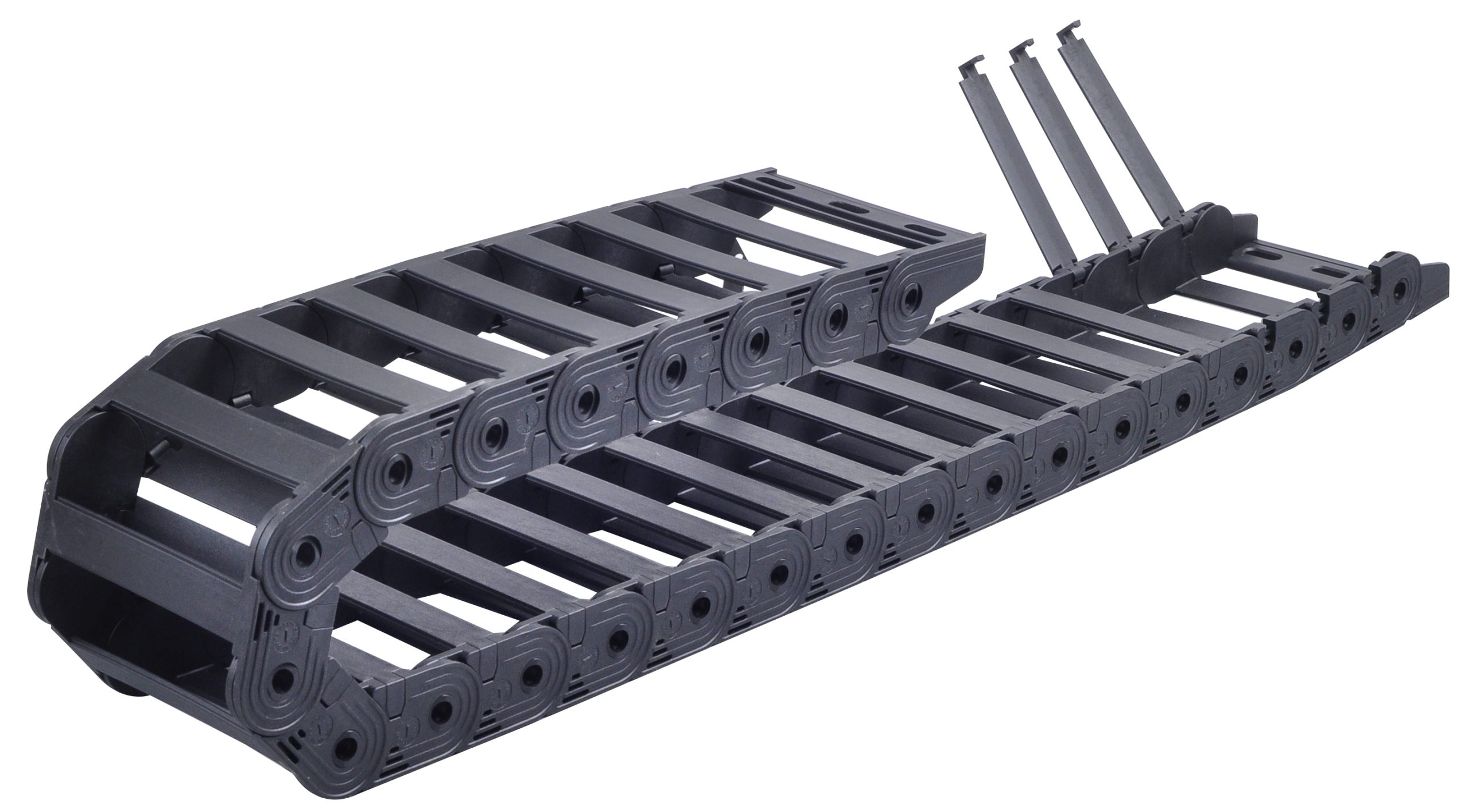
Key Factors Affecting Corrosion Performance
Material | Best For | Weakness | Certifications |
---|---|---|---|
Carbon Steel | Dry environments | Rusts quickly | ISO 9001 |
Stainless Steel | Chemical exposure | Costly | FDA compliant |
Nylon | Moisture resistance | Low heat tolerance | REACH, RoHS2 |
PPA Plastic | Moderate acids/oils | Brittle in cold | UL94 HB |
Plastic drag chains (like our DOWE PPA series) work for 80% of applications, but always request material test reports. I once had a client in Saudi Arabia needing chains for desalination equipment – we used 316L stainless3 with titanium coating4.
How Do Environmental Factors Impact Material Choice?
Your factory floor isn’t a lab. Real-world conditions like temperature swings and mechanical stress accelerate corrosion.
Saltwater environments degrade carbon steel 5x faster than dry settings, while UV exposure cracks nylon chains. Always map your operating conditions before selecting materials.
Corrosion Accelerators Ranked
- Chlorides (e.g., coastal/marine areas) 🌊
- Acids (pH <4 reduces steel lifespan by 70%) ⚗️
- High humidity (>80% RH) 💧
- Abrasive particles 🏭
Our team uses this simple formula:
Corrosion Risk = (Chemical Exposure × Temperature) ÷ Maintenance Frequency
Can Coatings Improve Existing Drag Chains?
Yes, but with caveats. Electroplating adds 2-3 years to steel chains, while polymer coatings suit plastic upgrades.
Zinc-nickel plating boosts steel’s saltwater resistance by 40%, but increases costs by 15%. For budget-conscious buyers, epoxy coatings offer decent short-term protection.
Coating Type | Cost Increase | Lifespan Boost | Best Paired With |
---|---|---|---|
Electroplating | 15-20% | 2-3 years | Steel chains |
Polymer Spray | 5-8% | 1-1.5 years | Plastic chains |
Ceramic Layer | 25-30% | 4+ years | Stainless steel |
Pro Tip: We provide free coating recommendations for DOWE chain buyers. Last quarter, a German automotive client combined our PPA chains with anti-static coating – zero corrosion issues in their electrocoating line.
How to Verify Material Certifications? (Avoid Pranav’s Mistake)
Pranav learned the hard way – 30% of suppliers falsify test reports. Always validate these 3 documents:
- Mill test certificates (traceable to raw material batch)
- Third-party corrosion test reports (ASTM B1175 salt spray test)
- Compliance statements (REACH/RoHS for EU exports)
Legitimate suppliers provide original test samples. We ship 50cm material samples with every quote – test them in YOUR environment.
Conclusion
Plastic drag chains win for general use, stainless steel for harsh chemistry. Match materials to your environment, verify certifications, and plan maintenance. Your chains should outlast your machinery.
- PPA (Polyphthalamide) offers superior resistance to oils and moderate acids compared to standard plastics. ↩
- REACH/RoHS compliance ensures materials meet EU safety and environmental regulations. ↩
- 316L stainless steel contains molybdenum for enhanced chloride resistance, critical for marine/chemical applications. ↩
- Titanium coatings create an oxide barrier that prevents pitting corrosion in stainless steel. ↩
- ASTM B117 is the industry-standard accelerated corrosion test simulating years of environmental exposure. ↩