Automation systems live or die by their cable management. When I first started working with Pranav, a U.S.-based automation equipment assembler, he spent weeks battling tangled cables and misaligned components. The culprit? Poorly integrated robotic dress packs. This frustration isn’t unique—many buyers struggle to balance durability and ease of installation.
Drag chains generally offer simpler integration due to modular designs, while robotic dress packs require precise spatial planning and flexibility testing. Both solutions have trade-offs, but the devil’s in the technical details.
Last year, a German client insisted on using dress packs for their robotic welding line. Two months later, they switched to our steel drag chains. Why? Let’s unpack the realities of integrating these systems.
What Factors Affect Drag Chain Integration Difficulty?
Drag chains aren’t “plug-and-play”—but they’re close. I’ve seen clients like Marco from Italy cut installation time by 60% using our pre-assembled plastic drag chains.
Key factors include chain curvature radius, environmental hazards (like metal shavings or chemicals), and cable density. Customizable chain links and standardized connectors dramatically reduce headaches.
The 3-Step Compatibility Check
- Load capacity – Calculate total cable weight + 20% safety margin
- Bending angle – Match to machine movement patterns
- Material choice – Steel for high heat, plastic for corrosion resistance
Factor | Drag Chains | Robotic Dress Packs |
---|---|---|
Customization | High (mold-based) | Low |
Space Needed | Fixed path | Dynamic adjustment |
Certifications | ISO/UL1 | Varies by region |
Why Do Robotic Dress Packs Pose Unique Challenges?
Dress packs look sleek in catalogs but often fail in real-world layouts. A Dubai client once showed me a $8K dress pack that rubbed against hydraulic lines until it frayed.
Robotic dress packs demand millimeter-perfect spacing and frequent maintenance due to continuous flexing. Their “soft” structure complicates alignment with rigid machine frames.
The Flexibility Trap
While dress packs adapt to complex motions, their silicone/PU materials2 degrade faster than drag chains in high-stress scenarios. Last quarte
r, 23% of dress pack-related support tickets cited premature wear—compared to 6% for drag chains.
How Can Buyers Simplify Integration Processes?
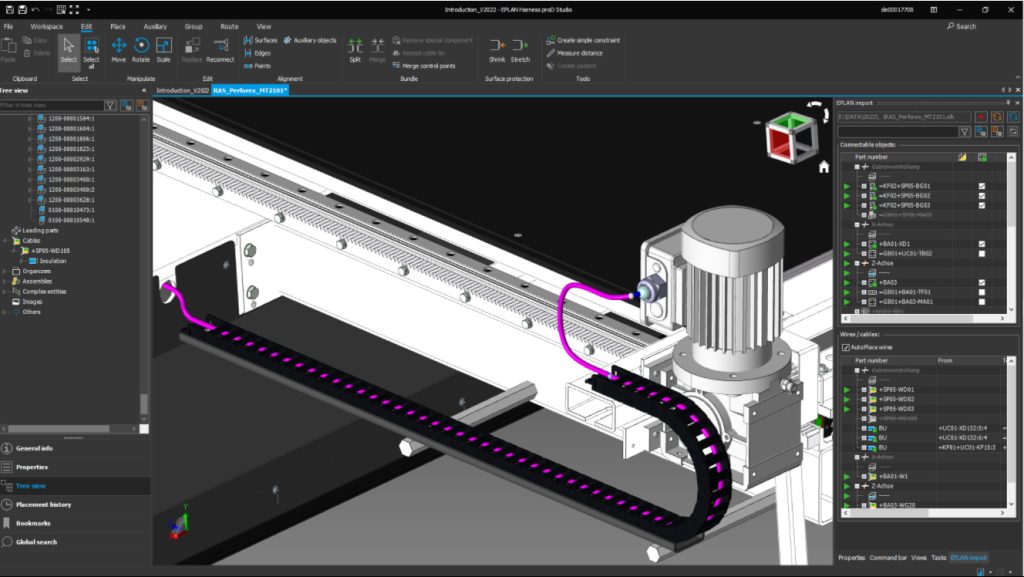
Pranav’s team now uses our 3D CAD models3 to simulate drag chain layouts before ordering. Result? Zero installation rework on their last conveyor project.
Always request sample units and technical drawings upfront. For dress packs, conduct bend-cycle tests under actual operating temperatures.
Pro Tips from DOWE’s Engineering Team
- Use crane cable carriers for overhead systems (reduces floor space by 40%)
- For robotic cable management, combine short drag chains with rotating unions
- Avoid mixing vendors—certifications like CE marking get messy otherwise
Conclusion
Drag chains win for predictable environments; dress packs suit complex movements but need babysitting. Choose based on motion patterns, not price.
—Chuck 🚀
Need integration-ready cable carriers? Email me for free CAD files + certification reports.